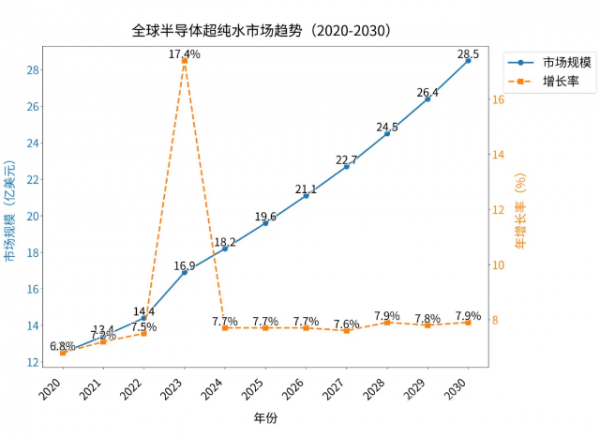
设备冷却:半导体生产过程中,一些设备会产生大量热量,需要超纯水进行冷却,以维持设备的正常运行温度,确保生产过程的稳定性和设备的使用寿命。
不同规模的半导体制造商对超纯水的需求存在差异。小型制造商每月用水量可能在数千立方米,而大型制造商每月用水量可达数万立方米甚至更多。例如,生产一片8英寸(直径200mm)的晶圆需消耗约5.6吨超纯水。而超纯水产出效率往往不足65%,约6,000升原水才能产出3,800升超纯水,也就是说,生产一片8英寸的晶圆实际上需要消耗近9吨水!台积电作为全球最大的芯片代工制造商,一年生产约1600万片12英寸晶圆,用水约1亿立方米,相当于一个200万人城市1年的用水量。
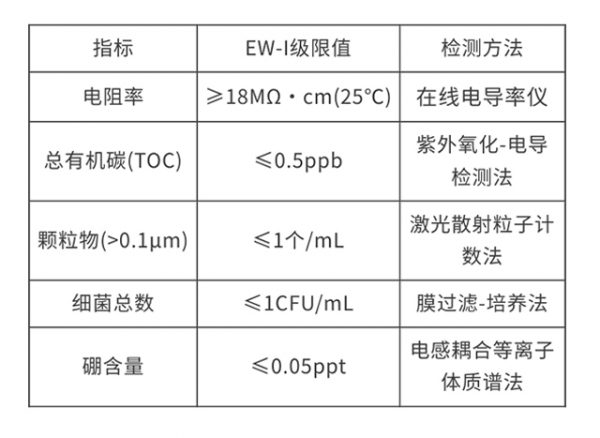
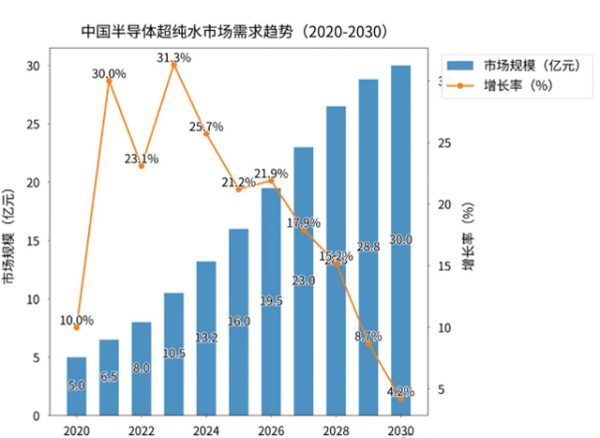
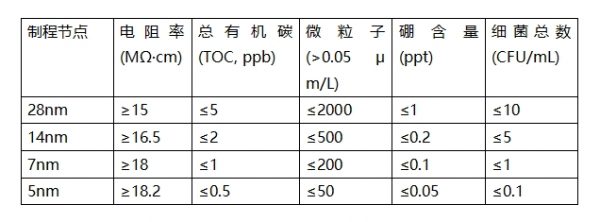
2.EDI及一级RO浓水回收技术
原理:采用高效反渗透技术,对EDI(连续电除盐)和一级RO(反渗透)过程中产生的浓水进行处理。在压力作用下,浓水中的水分子通过反渗透膜,而大部分盐分和其他杂质被截留,从而实现浓水的回收利用。
优势:一级RO浓水回收率可达60-70%,提高了水资源的利用率,降低了制备成本。
3.划片废水回收技术
原理:利用多介质过滤器,对划片废水中的悬浮物颗粒物等进行过滤和截留,同时去除部分有机物和微生物,使处理后的废水达到回到原水箱继续使用的标准。
优势:有效地减少了划片废水的排放,降低了对环境的影响同时节约了水资源。
4.自由端超滤技术
针对问题:切片废水因悬浮物高、含细硅粉颗粒,传统超滤存在死角大、布水不均匀、无法对膜丝有效冲刷、系统内湍流较弱等问题,导致堵的快。
原理:自由端膜丝未封装固定,可自由抖动,大幅度增加曝气冲刷效果,自由式端口使污染物不易聚集,便于排出,清洗死角少,延缓膜污染。专利制膜配方使膜丝具有高通量抗污染特性,模块化设计易于安装更换,适配性强,开放式流道设计,定制运行工艺可实现高回收率低药洗频率。
优势:解决了传统超滤在处理切片废水时的堵塞问提高了超滤系统的运行效率和稳定性,减少了维护成题。
5.Mesh MABR复合膜技术
原理:求是膜专利技术的复合MABR膜,克服了常见膜如疏水微孔膜(PTFE、PVDF、PP、PE)的膜孔污染、水压影响扩散效果、控制难和无孔致密膜(PMP)的产业化难、气体传输阻力大、强度低等缺点,通过特殊的结构和材料设计,实现高效的气体传输和水质净化。
优势:提高了膜的使用寿命和处理效率,降低了运行成本,适用于多种复杂水质的处理。
6.膜软化装置
原理:膜软化一体化装置可用于除硬、除硅、除氟、除各类重金属离子,各类高悬浮物固液分离及含油复杂废水处理。其工作原理是利用特殊的膜材料和处理工艺,选择性地去除水中的硬度离子(如钙离子、镁离子等)和其他杂质。
优势:适用于中小规模水处理系统,安装简便,施工周期短,能够有效降低水的硬度和杂质含量。
7.PolyMesh系列-膜脱气技术(膜法除氧、膜法脱碳、膜法脱氨)
膜法除氧原理:将水体中的溶解氧降低至1ppb以下:满足半导体等行业对脱氧水制备的需求。其原理是通过特定的膜材料和操作条件,使水中的溶解氧在压力差或浓度差的作用下透过膜,实现与水的分离。
膜法脱碳原理:在超纯水制备中脱除二氧化碳,降低后道耗材负担延长寿命;在半导体纯水中精确控制二氧化碳含量,实现无添加控制电导率。其工作原理是利用膜对二氧化碳的选择性透过性,将水中的二氧化碳从液相转移到气相,从而达到脱除二氧化碳的目的。
膜法脱氨原理:利用脱气膜透气不透水的性质,将高氨氮废水中的游离氨通过跨膜吸收转化为铵盐溶液或氨水,将废水中氨氮降低到15ppb以下。该技术通过调节废水的pH值使铵离子转化为游离氨,然后在膜两侧的浓度差作用下,游离氨透过膜被吸收液吸收并转化为铵盐。
优势:在超纯水制备过程中有效地去除水中的溶解气体,提高超纯水的纯度和质量,满足半导体行业对超纯水水质的严格要求。
8.TOC相关技术
直接电导法TOC技术原理:水系统样品经进样口进入仪器后,通过调节阀调节进样压力,流量计监测到稳定流量的样品,流经1C电导池后,获得IC信号,进入紫外氧化反应器进行充分氧化后,再流经TC电导池,获得TC信号后将样品排出仪器。根据公式:TOC=TC-IC,计算得到样品中总有机碳的浓度。
薄膜电导法TOC技术原理:蠕动泵抽取待测样,进样器添加试剂后将样品分为两路。一路样品通过氧化反应器和氧化剂将样品中的有机物完全氧化成二氧化碳,另一路样品则不氧化,将样品本身含有的二氧化碳作为背景。两路样品通过膜过滤模块将二氧化碳传递至内循环,再经电导池检测其电导率变化。根据公式:TOC=TC-IC,最后得出样品中总有机碳的浓度。
9.微生物检测技术
技术原理:微生物含有NADH和核黄素等代谢物,当暴露于特定波长的光线下,会发出荧光。利用激光诱导荧光技术进行检测,通过检测荧光信号的强度来确定水中微生物的含量。
(三)特种树脂制备超纯水
1.产品优势
流程优势:相比于现有的制水系统,流程简,省空间;压力小,能耗低;废水少,产水高;价格低,省成本;产水精,能达到电子行业对超纯水的要求。
树脂优势:所采用的越琦电子级离子交换树脂,可直通自来水得到超纯水。在实验室实验中,得到的超纯水的电导率能够达到0.052uS/cm,能够满足电子行业需求。在处理电导率30uS/cm以下水质,体积运行比在1:1000以上,运行稳定。硬度为300uS/cm的原水可以直接进树脂,所得到的超纯水的品质能够满足电子、医药、实验等行业需求,甚至可以应用于更高层次行业的用水需求。
2.工艺流程:包括油相的清洗、磺化、清洗、碱化,合成白球,脱水,水相包装等。